Biodiesel Production Plant
Biodiesel Production Plant
Biodiesel refers to a vegetable oil or animal fat-based diesel fuel consisting of long-chain alkyl (methyl, ethyl, or propyl) esters. Biodiesel is typically made by chemically reacting lipids (e.g., vegetable oil, animal fat) with an alcohol producing fatty acid esters.
Biodiesel is meant to be used in standard diesel engines and is thus distinct from the vegetable and waste oils used to fuel converted diesel engines. Biodiesel can be used alone, or blended with petrodiesel in any proportions. Biodiesel can also be used as a low carbon alternative to heating oil.
A complete biodiesel production plant mainly contains fellowing steps: Seed storage, Oil extraction, Catalytic conversion to biodiesel, By-product processing, Process and plant support systems.
The Chemical Process of the Biodiesel Production Plant: The fat or oil is combined with an alcohol such as methanol in the presence of a catalyst in a reactor. This reaction occurs at low temperatures (room temperature to about 140 degrees F) and low pressure and produces a crude biodiesel and glycerin . Once the reaction is complete, the glycerin, which is denser, is drawn off the bottom of the settling vessel. Next, the excess alcohol is removed from the biodiesel and from the glycerin and recovered by distillation. The biodiesel is further purified to remove residual catalysts and other contaminants and then dried. The biodiesel and glycerin are then pumped to storage tanks.
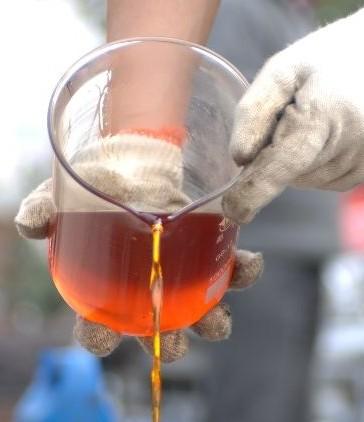
Biodiesel
Size of the Biodiesel Production Plant: A biodiesel production plant typically requires 15 to 80 acres for all the facilities. The total area of the site is usually larger, landscaped, and serves as an exclusion area to the public.